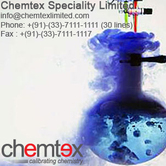
Propylene glycol [HO-CH2-CH(OH)-CH3] is pronounced as pro'puh-leen-gly'col. It is a clear, colorless, slightly syrupy liquid at room temperature. The compound may exist in air in the vapor form though it must be heated or briskly shaken to produce a vapor. It is actually a multi-variant chemical compound. Propylene glycol - in an industrial cooling and heating process terminology is referred as industrial coolant or heat transfer fluid (HTF) or the common fluid that is used in large installations for transporting heat from one place to another.
Features :
- serves as a solvent
- offers outstanding stability with high flash and boiling points
- reduces the freezing point
- increases the boiling point
- helps to bind and transport other substances (excipient)
- holds and dissolves active ingredients equally in a medium
- connects and stabilizes insoluble fluids (emulsifier)
- attracts/holds water/moisture (hygroscopic)
Usage :
- As an emulsification agent in Angostura and orange bitters
- As a moisturizer in medicines, cosmetics, food, toothpaste, shampoo, mouth wash, hair care and tobacco products
- As a carrier in fragrance oil
- To produce polyester compounds
- As a base in deicing solution
- In smoke machines to make artificial smoke for use in firefighters' training and theatrical productions
- As a solvent for food colors and flavorings
- As an ingredient, along with wax and gelatin, in the production of paintballs
- As a wetting agent, used to determine drying time in paints and coatings
A non-toxic substitute of Ethylene Glycol :
Propylene Glycol is the replacement of Ethylene Glycol in newer automotive antifreezes and de-icers in aircrafts. Like Ethylene Glycol, Propylene Glycol also has the special physical characteristics of depression of freezing point when mixed with water. It happens due to disruption of hydrogen bonding. Pure water freezes at 0OC. But aqueous solution of Propylene Glycol (10% by weight) has a freezing point of -3OC. 30% by weight aqueous solution of Propylene Glycol freezes at -12OC and a 60% by weight Propylene Glycol and water mixture can further lower down this freezing point to -51OC.
Why Glycol turned into red color ?
Because of the extensive corrosion & rust in the system metal makes the glycol turn reddish in color. At this point the glycol is fouled with iron contaminants that increase the glycol degradation rate. It is important to add corrosion inhibitor to the glycol system to avoid such degradation of glycol.
Application Areas :
Beverages & Juices, Breweries & Distilleries, Packaged Food Freezing, Canneries & Preservers, Fish Processing Units, Pharmaceutical & Bulk Drugs, Poultry Processing Industry, Thermal Storage System, Heating and Cooling Systems, Snow Melting and Refrigeration, Ice Skating Rinks, Vegetable Oil Industry, Ice Manufacturer, Cold Storage Systems etc.
Product Physio-Chemical Data :
- Form and Appearance - Clear, colorless liquid
- Assay as Propylene Glycol - 99.8%
- Specific Gravity - 1.04 (approx.)
- Molecular Wt. - 76.0548 gm/mol
- Solubility in Water - 100%
Handling Measures, Precaution & Storage :
Propylene Glycol is slightly hygroscopic & the storage temperature is not critical, it must be stored under conditions so that contamination with water and adsorption of moisture are prevented. It should be noted however for product quality reasons the storage temperature should not go above 40°C. At below freezing temperatures the product viscosity might become too high for transfer from the storage containers with the pumps available. PG is a stable chemical and is not expected to deteriorate significantly with time provided if it is stored as indicated. The drums should be stored in dry condition, better to use the original drums rather than the other drums and if the drums are opened then it must be closed tightly at unused situation. The chemical can be stored up to 6 months.